Specialist Packaging Machine Repair Service to Maintain Your Tools Running Efficiently
Specialist Packaging Machine Repair Service to Maintain Your Tools Running Efficiently
Blog Article
Understanding the Secret Components and Fixing Techniques for Product Packaging Equipment Upkeep
Efficient maintenance of product packaging equipments hinges on a detailed understanding of their essential components, consisting of the framework, drive system, and securing systems. Identifying common upkeep problems, paired with the execution of preventative techniques and fixing strategies, can considerably boost machine integrity. Moreover, the selection of fixing methods, including using OEM parts and the importance of qualified service technicians, plays a critical role in reducing downtime. To really realize the complexities of these systems and their maintenance, one should think about the wider implications of disregarding these necessary methods.
Key Parts of Product Packaging Devices
Product packaging makers contain several key parts that work together to make sure efficient and efficient packaging procedures. At the core of these makers is the framework, which provides architectural integrity and houses the various operating components. The drive system, often a combination of motors and gears, promotes the activity of parts, allowing specific operation throughout the product packaging cycle.
An additional essential element is the conveyor system, which delivers items through various stages of the product packaging process. This is commonly matched by sensors and controls that keep an eye on the setting and rate of things, making certain synchronization and minimizing errors. The loading system is critical for precisely dispensing the ideal amount of product right into plans, whether in fluid, powder, or solid form.
Securing systems, including heat sealants or adhesive applicators, play an important role in securing packages, stopping contamination and expanding life span. Additionally, identifying systems are integral for offering needed item info, making sure conformity with regulations. Lastly, the control board, geared up with easy to use interfaces, allows operators to take care of maker functions, display efficiency, and make adjustments as needed, guaranteeing ideal productivity and efficiency in packaging procedures.
Common Upkeep Problems
Reliable procedure of packaging makers counts heavily on regular maintenance to protect against common problems that can interrupt manufacturing. Amongst these issues, mechanical wear and tear is common, specifically in parts like seals, motors, and conveyors, which can result in unforeseen downtimes. In addition, imbalance of parts can result in inefficient operation, triggering products to be improperly packaged or harmed throughout the procedure.
An additional common maintenance issue includes the build-up of dust and debris, which can disrupt the device's sensing units and relocating components. packaging machine repair service. This not just impacts efficiency yet can additionally posture security risks. Lubrication failings can lead to boosted rubbing, resulting in overheating and eventual element failure.
Electrical troubles, often originating from loosened links or worn-out wiring, can disrupt equipment functions, leading to substantial manufacturing delays. Software application glitches due to incorrect configurations or obsolete programs can impede the machine's operation, necessitating instant intervention. Attending to these common upkeep issues proactively is crucial for making sure optimal efficiency and longevity of packaging equipment.
Preventative Maintenance Approaches
Carrying out preventative upkeep methods is crucial for maintaining the performance and dependability of product packaging devices. These approaches encompass an organized approach to upkeep, concentrating on the routine inspection and servicing of tools to preempt potential failings. By adhering to a set up maintenance program, operators can identify wear and tear on elements before they cause substantial break downs.
Key elements of a preventative upkeep strategy include regular examinations, part, lubrication, and cleansing substitutes based upon manufacturer suggestions. Using lists can simplify this procedure, making certain that no vital tasks are ignored. Additionally, preserving exact records of maintenance activities aids in tracking the device's performance gradually, assisting in notified decision-making relating to future maintenance requirements.
Educating staff on the value of preventative maintenance enhances conformity and promotes a culture of proactive care. Applying an anticipating upkeep element, utilizing data analytics and sensor modern technology, can better optimize machinery performance by forecasting this link failings prior to they happen.
Fixing Methods
When confronted with breakdowns or inadequacies in packaging machines, using methodical troubleshooting techniques is crucial for determining and fixing issues swiftly. The primary step in efficient troubleshooting is to develop a clear understanding of the machine's functional parameters and efficiency metrics. This includes evaluating the device's specs, as well as any kind of error codes or notifies displayed.
Next, operators must conduct an aesthetic assessment, looking for noticeable signs of damages, wear, or imbalance. This typically consists of checking out sensing units, belts, and gears to pinpoint prospective reasons for malfunction. Gathering functional information, such as production rates and downtime logs, can also give understandings into reoccuring problems.
When potential issues are identified, using a rational technique to separate the origin is essential. This may require testing individual components or systems in a controlled fashion. Participating in discussions with operators who connect with the equipment consistently can generate beneficial responses concerning uncommon habits or patterns.

Repair Service and Substitute Best Practices
A detailed understanding of fixing and substitute best methods is essential for keeping the durability and effectiveness of packaging machines. Routinely evaluating the problem of maker parts allows for prompt treatment, protecting against more substantial issues that can cause costly downtimes.
When repairs are necessary, it is important to use OEM (Original Tools Supplier) parts to make sure compatibility and efficiency. This not only protects the stability of the machine but also promotes warranty contracts. Furthermore, it is advisable to preserve a supply of essential extra parts to facilitate quick substitutes and minimize functional interruptions.
For complex fixings, involving licensed technicians with specialized training in product packaging machinery is advised. They possess the expertise to detect issues properly and implement repairs effectively. Additionally, recording all repair tasks and parts substitutes is important for keeping a thorough upkeep background, which can aid in future troubleshooting.
Last but not least, applying an aggressive method, consisting of normal examinations and anticipating maintenance techniques, boosts the reliability of packaging makers. By sticking to these ideal practices, services can guarantee optimum machine efficiency, decrease operational risks, and extend tools life expectancy.
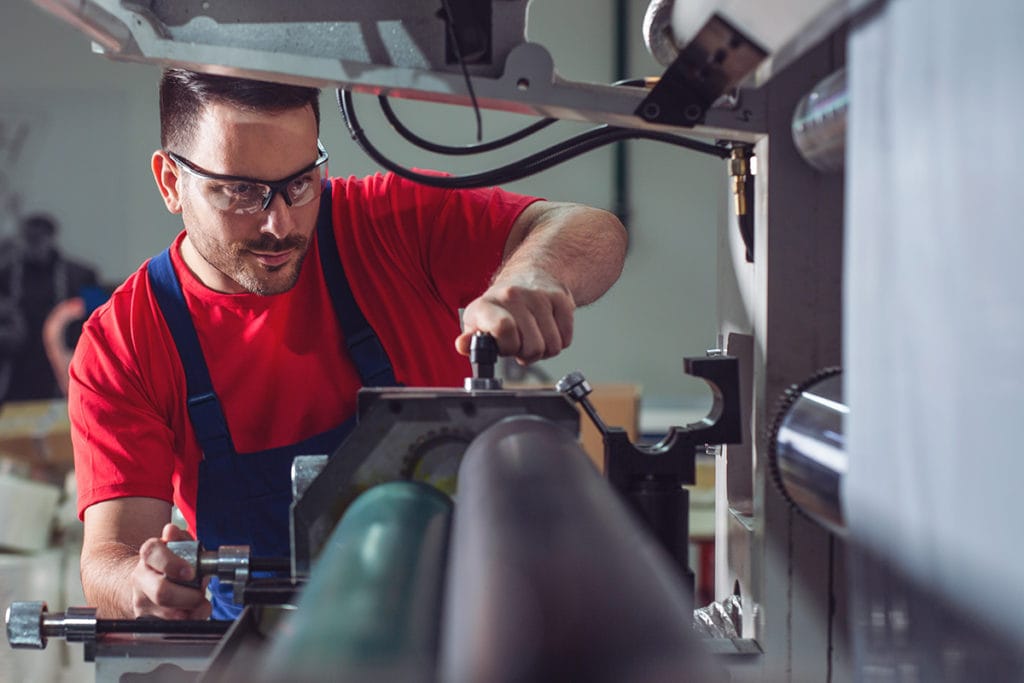
Verdict
In verdict, a complete understanding of packaging device elements and reliable upkeep strategies is crucial for optimum performance. Normal assessments and the use of OEM parts can dramatically decrease downtime, while a well-documented upkeep background cultivates proactive treatment. Using qualified specialists even more enhances repair quality and dependability. By implementing these practices, companies great post to read can ensure the durability and efficiency of packaging devices, eventually adding to enhanced operational efficiency and minimized costs.
Effective upkeep of packaging machines hinges on a complete see it here understanding of their crucial components, consisting of the frame, drive system, and securing mechanisms.Reliable procedure of product packaging devices depends heavily on regular maintenance to avoid typical problems that can interfere with production.Implementing preventative maintenance techniques is important for maintaining the effectiveness and dependability of packaging machines. In addition, keeping precise documents of maintenance tasks aids in tracking the maker's performance over time, assisting in informed decision-making relating to future maintenance needs.

Report this page